You've worked out which machine will suit what you're wrapping, now it's time to look at which type of film carriage you need.
There are two main types of wrap head / film carriage: the first is what we call a post-stretch film carriage, the next, a pre-stretch film carriage. The pre-stretch carriages are more expensive but often make more financial sense long term.
Post-Stretch
A post-stretch film carriage essentially applies a brake to a roller and makes the film more difficult to pull off of the film carriage. When this happens, the film gets stretched slightly further - like stretching a piece of gladwrap between your hands.
Post-stretch machines are ideal for wrapping heavy products like a bags of cement, bags of flour, concrete blocks or bricks, working best with heavy products where the film tension won't pull layers off the pallet.
These machines also work well for low throughput operations to save staff running around holding the roll of stretch wrap, helping speed up the process slightly and make things a lot easier.
Pre-Stretch
If you're wrapping higher quantities of pallets or very lightweight products - a pre-stretch machine is usually the better option. These machines have an individually adjustable force-to-load ratio so you can have them set to pull tightly on the pallet or just lay the wrap on with very little force.
Through the pre-stretch process, the film will retain a memory of its original state, so once on the pallet, it keeps the load very secure as it tries to pull back together. The powered pre-stretch operates by a motor that controls a couple of geared rollers systems. The film comes off the bulk reel, goes around the ramp head then across the pallet rollers.
Different pre-stretch heads are capable of different levels of stretching. Our standard wrap head is capable of 240% pre-stretch, but our available wrap heads range is capable of anywhere from 30% to 400% depending on what you're wrapping.
Pre-stretch machines save you money by reducing the number of bulk rolls of pallet wrap you need to buy.
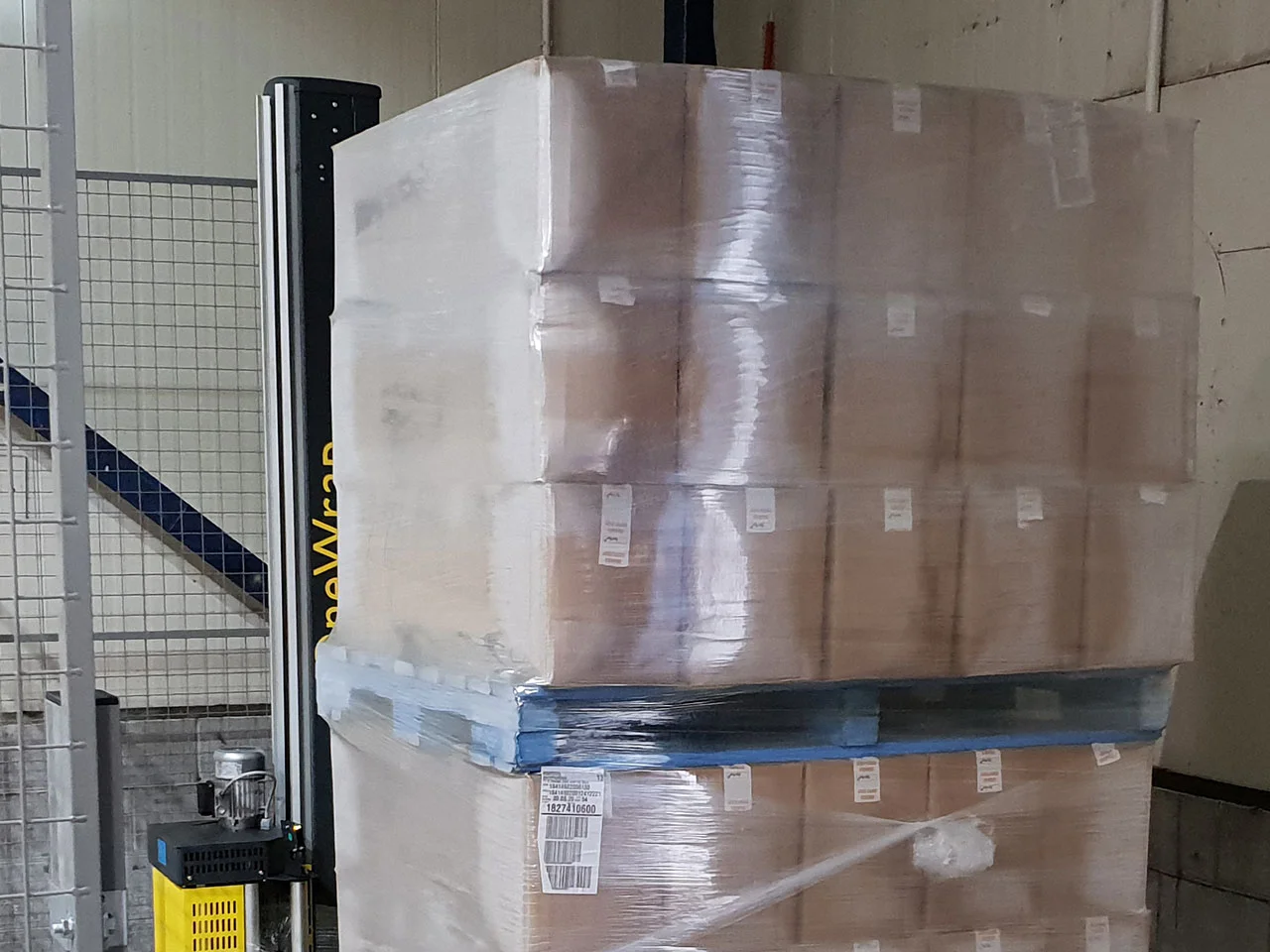
Post-Stretch vs Pre-Stretch
So on a post-stretch wrap head, there's very little stretching involved. Using one kilometre of wrap film will wrap only one kilometre of pallet perimeters before you run out of film.
With a pre-stretch wrap head, the stretch percentage is how much it increases the length of your wrap by. So with a 240% pre-stretch head, suddenly a one-kilometre roll of film will allow you to wrap 3.4 kilometres of pallet perimeters.
So if the two machines were running side-by-side, the pre-stretch would wrap three times as many pallets as the post-stretch with the same amount of film, saving you a lot of money on operating costs in the long run.
Pre-stretch stops Neckdown
Neckdown: the narrowing of stretch-film as it stretches around a load or pallet.
A potential problem with the Post-stretch wrap heads is, as film stretches between the pallet and machine, the film becomes longer, thinner, and loses width. Losing width requires each round of wrap to be closer together, taking that many more revolutions of film to give a secure hold. A conventional 500mm wide roll could end up being 350mm wide on the pallet.
Neckdown is a problem you can avoid with the use of a pre-stretch film head. The powered stretching of the film within the wrap head, ensuring the stretched film is the same width as when it comes off of the roll - keeping the number of rotations required to wrap a pallet minimal and saving costs on stretch film.
Next Article:
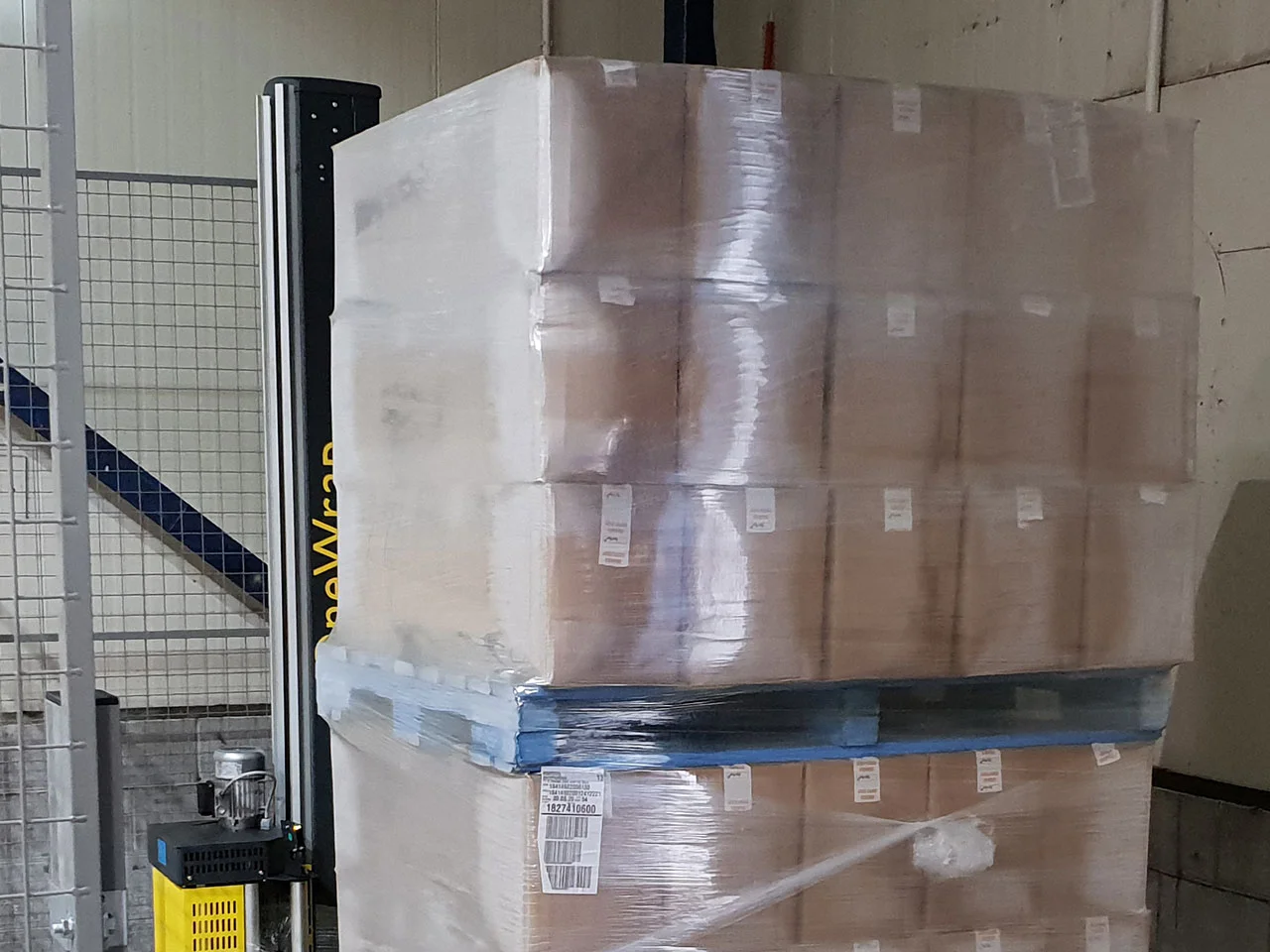